Tariffs Disrupt Food Supply Chains: How Companies Are Navigating New Challenges
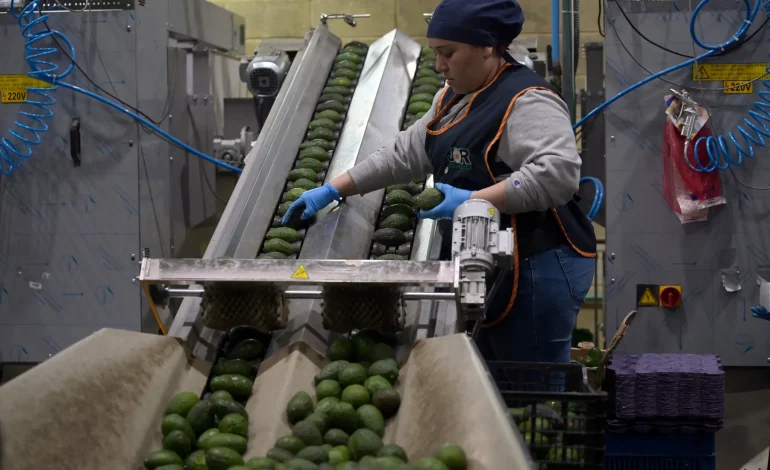
Companies strengthened their supply chains in response to the pandemic, ensuring more flexibility and resilience, the New York Times reports.
However, the new wave of tariffs imposed by the Trump administration is adding an unforeseen challenge, testing how well these systems can withstand additional shocks.
Victoria Gutierrez, the chief merchandising officer for Sysco, a global food distributor with nearly $79 billion in annual revenues, has been carefully monitoring the impact of tariffs on the company’s vast network of suppliers. In anticipation of tariffs, Sysco’s task force reviewed which products could be affected, particularly fresh produce from Mexico, Canada, and China. With the pandemic already having forced changes in global supply chains, companies like Sysco had already diversified and even duplicated suppliers for critical goods.
However, certain products, like avocados, present a unique challenge.
“The majority of avocados eaten in the United States come from Mexico. Can we today meet the full demand for avocados in the US? No,” Gutierrez noted.
There is simply not enough domestic production of avocados in the winter to meet the need. The tariffs, which include a 25% levy on imports from Canada and Mexico and a 20% tariff on Chinese goods, could exacerbate existing supply shortages.
In the face of these tariffs, Sysco has been working to build up inventories of non-perishable items or seeking alternative suppliers from countries not impacted by tariffs. For instance, Will Ford, COO of Westrock Coffee, shared that the company was already looking to shift some coffee sourcing from Mexico to Central American countries like Honduras or Guatemala to avoid tariff-related costs.
The challenge intensifies with perishable products such as avocados, where companies must either absorb the additional tariff costs or pass them on to consumers. Major brands like Chipotle are choosing to absorb the costs for now, but other companies, like Target, are already warning consumers of potential price hikes on products like fruits and vegetables from Mexico.
For some companies, the choice to diversify suppliers in response to the pandemic proved beneficial. Mondelez International, for example, relies on its Salinas, Mexico, factory for key snack items like Oreo cookies and Ritz crackers. However, the cost-efficient production at that facility may be compromised by the tariffs, making repatriating production to the US challenging and costly.
Food and beverage companies are not the only ones feeling the pinch. Alcohol brands like Diageo, which imports tequila and liquors from Mexico, and Constellation Brands, which relies heavily on beer imports from Mexico, have expressed concerns about the financial hit from tariffs. Diageo has stated that it is exploring supply chain mitigation strategies to reduce the financial impact.
Despite these challenges, companies like Sysco are taking steps to adapt. While they continue to manage climate-related disruptions and the volatility of ingredient prices, they are also adjusting to the new reality of tariffs. As Gutierrez puts it:
“Uncertainty and dealing with shocks to the system is the name of the game.”
Whether through shifts in geography or strategy, companies are finding ways to adapt to both climate and trade-related disruptions.
The latest news in your social feeds
Subscribe to our social media platforms to stay tuned